Understanding Tube Fitting Dimensions for Optimal Performance
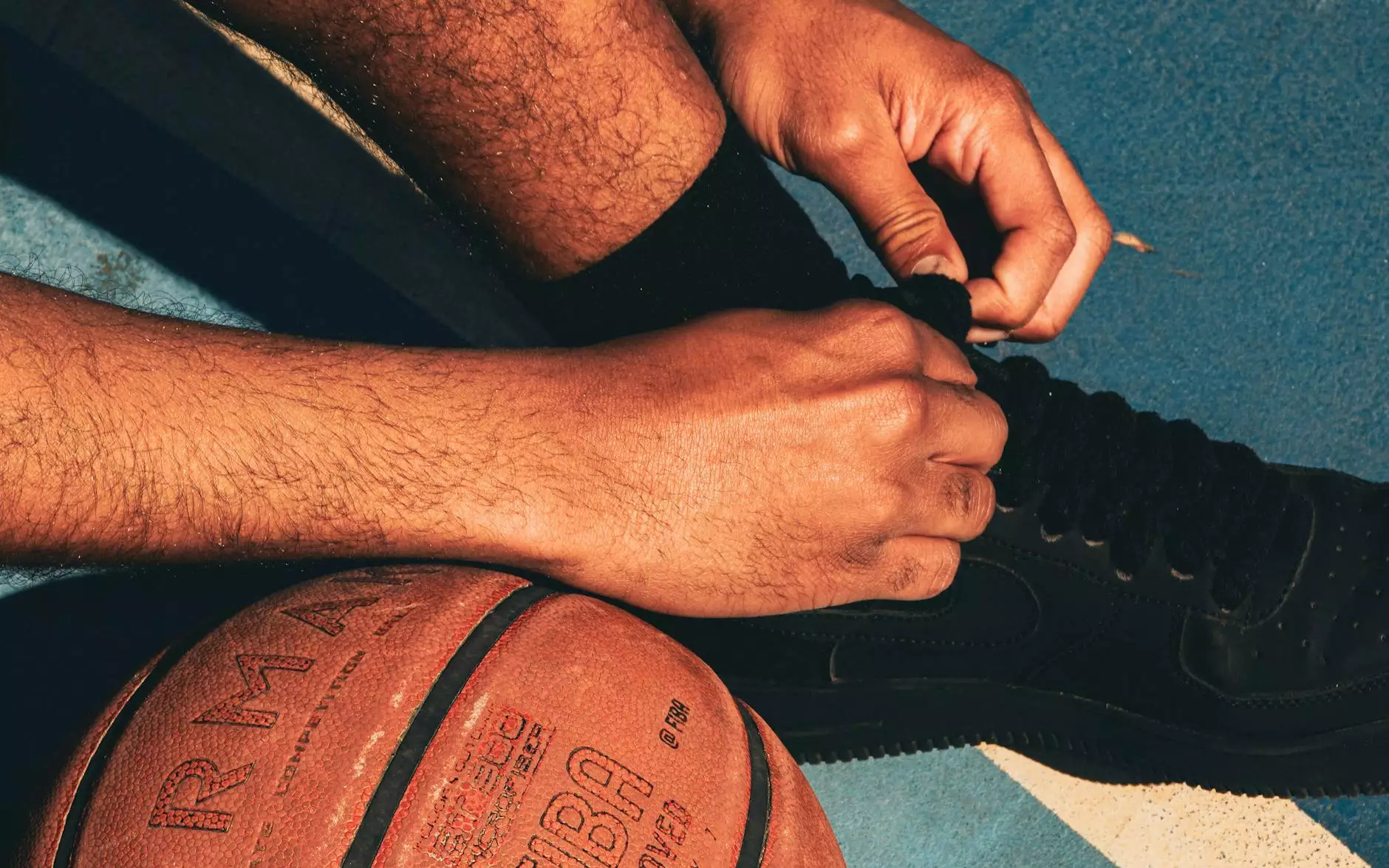
In the world of industrial applications, tube fitting dimensions play a crucial role in ensuring the functionality and reliability of piping systems. Whether you are involved in the construction of a new system or maintaining an existing one, understanding fitting dimensions is fundamental for efficiency and effectiveness.
What Are Tube Fittings?
Tube fittings are essential components in piping systems, used to connect, disconnect, or regulate the flow of fluids. They come in various forms and sizes, providing versatility across multiple industries, including manufacturing, oil and gas, pharmaceuticals, and water systems.
Importance of Accurate Tube Fitting Dimensions
Choosing the correct dimensions for tube fittings is vital for several reasons:
- Leak Prevention: Proper dimensions ensure tight seals, reducing the risk of leaks which can lead to fluid loss and safety hazards.
- Improved Performance: Accurate fitting dimensions optimize flow rates and pressure levels, enhancing the overall performance of the system.
- Compatibility: Ensuring dimensional accuracy guarantees that fittings are compatible with existing pipes and equipment, facilitating seamless integration.
Common Types of Tube Fittings and Their Dimensions
1. Ferrule Fittings
Ferrule fittings are crucial for creating reliable seals in tube connections. These fittings are characterized by their ability to compress a ferrule against the tube to form a leak-proof joint. Key dimensions include:
- OD (Outside Diameter): This is the external width of the tube that the ferrule will grip.
- ID (Inside Diameter): It is important for flow considerations.
- Ferrule Length: The length of the ferrule itself affects how much tube it will secure.
2. Forged Pipe Fittings
Forged pipe fittings are made from metal and provide robust connections in high-pressure applications. Their dimensions are vital for strength and stability.
- Socket Size: Refers to the fitting's end dimension for connection.
- Wall Thickness: Plays a role in the fitting's pressure rating.
- Connection Type: Common types include threaded and butt-weld fittings.
3. Threaded Pipe Fittings
Threaded pipe fittings are designed with threads on the ends for connecting to similarly threaded pipes. Dimensions that matter here include:
- Thread Pitch: Indicates the distance between threads.
- Nominal Pipe Size (NPS): A crucial measurement that dictates the size of the fitting.
Understanding NPT Fittings
NPT (National Pipe Tapered) fittings are commonly used for joining pipes in a variety of systems. Their tapered thread design allows for a secure and leak-proof fit, but proper specifications need to be observed.
- Diameter: Defined as the size of the pipe or fitting.
- Length of Threads: The effective engagement area of the fitting.
Measuring Tube Fitting Dimensions Accurately
To ensure the correct tube fitting dimensions, follow these steps:
- Use Calipers: For precision, use a digital caliper to measure outside and inside diameters accurately.
- Refer to Standard Specifications: Utilize industry-standard charts to cross-reference your measurements with standard fitting sizes.
- Consult Manufacturer Details: Always refer to the product specifications provided by the manufacturer for detailed dimension information.
How to Choose the Right Tube Fitting Dimensions
Choosing the right dimensions for tube fittings involves understanding the specific requirements of your application. Some considerations include:
- System Pressure: Higher pressures require fittings that can withstand greater forces. Check for pressure ratings that match your needs.
- Fluid Characteristics: Consider the type of fluids that will flow through the system, including their chemical compatibility with fitment materials.
- Temperature Limits: Ensure selected fittings can handle the operational temperature ranges.
Maintenance of Tube Fittings
Regular maintenance of tube fittings is crucial for ensuring their longevity and functionality. Here are some tips:
- Inspect Regularly: Frequently check fittings for signs of wear or damage.
- Replace Worn Parts: If any component exhibits wear, replace it immediately to prevent failures.
- Clean Connections: Remove debris and residue that may impair the seal or flow.
Conclusion
Understanding tube fitting dimensions is vital for any professional involved in the design and maintenance of piping systems. By prioritizing accurate dimensions, you can ensure optimal performance, reliability, and safety in your fluid transfer operations. For a comprehensive range of high-quality fittings, visit techtubes.in and discover solutions tailored to meet your project's needs.
Frequently Asked Questions (FAQs)
What are the most common tube fitting dimensions?
The most common dimensions include OD, ID, ferrule length, and thread size, as these directly affect the fitting's performance and compatibility.
How do I know which fitting is suitable for my application?
Always consider system pressure, fluid type, temperature limits, and the compatibility of the materials used in your pipes and fittings.
Can I mix different types of fittings?
It is strongly advised not to mix different types of fittings unless they are designed to be compatible, as this can lead to leaks.
Where can I purchase tube fittings?
You can browse through a wide range of tube fittings at authorized suppliers or online at techtubes.in.
What materials are commonly used for tube fittings?
Common materials include stainless steel, brass, and plastic, each suited for different applications based on their chemical resistance and pressure ratings.