The Ultimate Guide to Plastic Injection Mold Companies
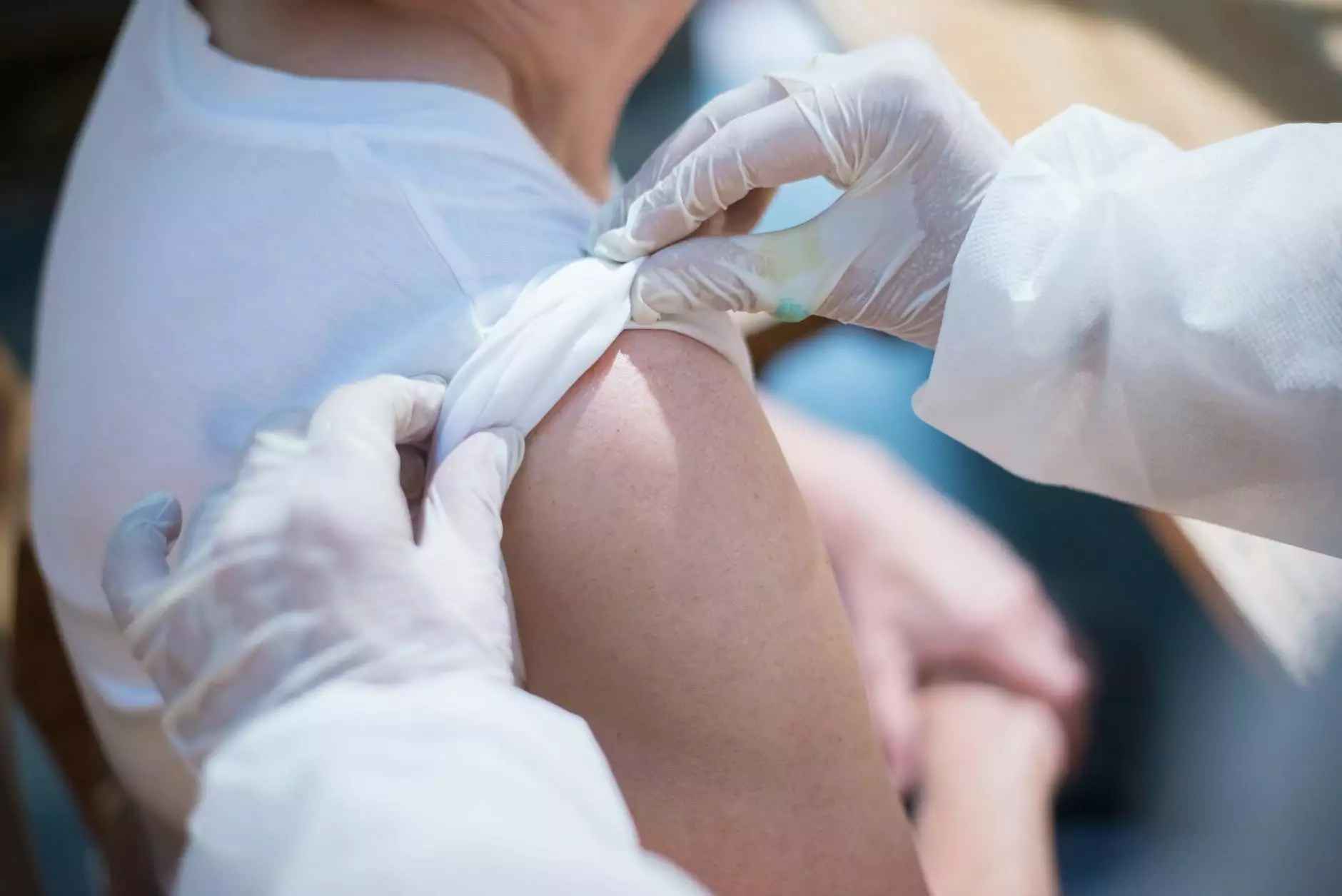
The world of manufacturing has evolved tremendously over the past few decades, and at the forefront of this transformation is the plastic injection mold company. These companies specialize in creating intricate molds used in the production of various plastic components, essential for numerous industries including automotive, consumer goods, electronics, and medical devices. In this article, we will delve deep into the fascinating world of plastic injection molding and the pivotal role these companies play in driving efficiency, quality, and innovation in modern manufacturing.
Understanding Plastic Injection Molding
Plastic injection molding is a manufacturing process that involves injecting molten plastic into a mold cavity, where it cools and solidifies into the desired shape. This method is favored for its efficiency and ability to produce high volumes of products with consistent quality. The process is highly automated, allowing manufacturers to achieve faster turnaround times and reduced labor costs.
How Does the Process Work?
The procedure of plastic injection molding can be broken down into several key stages:
1. Designing the Mold
The first step involves designing the mold, which can range from simple shapes to complex geometries. Experienced engineers at a plastic injection mold company utilize sophisticated CAD software to create detailed designs that meet specific product requirements.
2. Fabricating the Mold
Once the design is finalized, the next step is to fabricate the mold. This is typically done using metals like steel or aluminum, depending on the production volume and type of plastic used. The fabrication process requires precision machining to ensure the mold parts fit together seamlessly, ensuring high-quality production.
3. Preparing the Injection Molding Machine
After the mold is created, the injection molding machine is prepared. This involves heating the plastic pellets until they become molten and can be injected into the mold.
4. Injection and Cooling
The molten plastic is then injected into the mold under high pressure. After a short period, the plastic cools and solidifies, taking on the mold's shape. This cooling phase is critical, as it affects the finished product's dimensional accuracy and surface finish.
5. Ejection and Finishing
Once the plastic has cooled, the mold opens, and the finished part is ejected. Depending on the application, further finishing processes may be needed, such as trimming, painting, or assembly.
Advantages of Choosing a Plastic Injection Mold Company
Opting for a specialized plastic injection mold company comes with a myriad of advantages that can significantly impact your production outcomes:
- Cost-Effectiveness: The capability to produce large quantities of identical parts at a lower cost per unit makes injection molding an economically viable choice for manufacturers.
- Consistency and Precision: Advanced technology and automation ensure high precision, resulting in parts that meet stringent quality standards.
- Material Versatility: Injection molding can accommodate a wide variety of plastics, including thermoplastics, elastomers, and even some composites.
- Design Flexibility: Complex designs can be achieved that would be difficult or impossible to produce through other manufacturing methods.
- Reduced Waste: The injection molding process is efficient, and the majority of the plastic not used can be recycled.
Key Industries Benefiting from Plastic Injection Molding
Plastic injection molding is widely used across various industries, some of which include:
Automotive Industry
In the automotive sector, efficiency and reliability are paramount. Plastic injection mold companies supply components such as dashboards, bumpers, and fuel tanks. The ability to create lightweight yet durable parts contributes to fuel efficiency and performance.
Consumer Goods
From household items to personal care products, the consumer goods sector relies heavily on injection molding. Products that require aesthetic details, such as bottles and packaging, benefit from the intricate designs achievable through this process.
Electronics
The electronics industry requires high precision components that often integrate several functionalities. Injection molding allows for the production of parts such as connectors, enclosures, and circuit boards with precision and speed.
Medical Devices
In the medical field, the need for high-quality and compliant products is critical. Injection molding companies produce components for devices such as syringes, surgical instruments, and diagnostic equipment. The capacity for sterilization in production further enhances their usability.
Innovations in Plastic Injection Molding
As technology advances, so does the field of plastic injection molding. Here are some recent innovations shaping the industry:
3D Printing Integration
3D printing is being utilized to create complex mold geometries, allowing companies to produce molds more quickly and at a lower cost. This technology streamlines the prototyping phase and can lead to rapid design iterations.
Smart Manufacturing
The introduction of IoT (Internet of Things) in manufacturing makes it possible to monitor the injection molding process in real-time, leading to enhanced quality control and predictive maintenance.
Sustainability Initiatives
With a growing emphasis on sustainability, many plastic injection mold companies are exploring eco-friendly materials and processes. Biodegradable plastics and recycling programs are gaining traction, reducing waste and environmental impact.
Choosing the Right Plastic Injection Mold Company
Selecting the right plastic injection mold company is essential for the success of your project. Here are some tips to consider:
- Experience: Look for a company with a proven track record in your specific industry.
- Technological Capabilities: Ensure they have access to the latest technology, including advanced CAD and manufacturing equipment.
- Client Reviews: Check testimonials and case studies to understand their capabilities and customer service.
- Support and Communication: Good communication throughout the production process is vital. Choose a company that prioritizes client engagement.
- Quality Assurance: Inquire about their quality control processes to ensure that your products meet industry standards.
Conclusion
The role of a plastic injection mold company in today's manufacturing landscape cannot be overstated. As industries continue to evolve, the advances in injection molding technology will only enhance the capabilities of manufacturers, driving efficiency and innovation. By partnering with a knowledgeable and experienced injection molding company, businesses can ensure they remain competitive in a fast-paced market. With a solid understanding of the process and benefits, companies can make informed choices that lead to successful product outcomes.
For further inquiries into how a plastic injection mold company can add value to your manufacturing process, visit deepmould.net for more information.